With much of the Netherlands below sea-level, engineers who want to build underground garages and railway tunnels face many problems – not least how to construct sturdy retaining walls that stand up to the pressure of water and soils deep underground.
One way to tackle this particular challenge is to build so-called diaphragm walls, which are made of overlapping panels of reinforced concrete. “Diaphragm walls are potentially ideal retaining walls for deep excavations in densely built up areas,” said civil engineer Dr. Rodriaan Spruit, “because they can extend 40 metres underground, but you don’t cause vibrations in nearby buildings when you build them.”
What you do get with diaphragm walls however are leaks: around 1 in 6 projects suffers a severe leak, and often with disastrous consequences. For instance, in late 2009, a row of 17th century houses subsided by 14 centimetres as a result of a leaking diaphragm wall, which was part of Amsterdam’s new metro construction project. The problem lies with “the uncertain quality of the joints between panels” as Spruit rather delicately put it in his thesis. So, of course, any way of finding any weak points before construction gets underway would be a great help; hence Spruit’s doctoral thesis entitled “Detecting Anomalies in Diaphragm Walls”.
The main focus of Spruit’s research was to look at different ways of determining the quality of concrete in the area around the joints. Of the four techniques examined, Spruit found that Distributed Temperature Sensing (DTS), and particularly Crosshole Sonic Logging (CSL), were the most usable. “CSL determines how long it takes for ultrasound to travel between a source and receiver,” said Spruit, “and also the degree of signal loss.” The sound source and receiver are attached to the outer corners of the reinforcement cage, which is used in the construction of a diaphragm wall. And because the speed of sound depends on a medium’s density and stiffness, any potential problems, such as pockets of clay or soil within the concrete, give an ultrasound profile that’s different from pure concrete. Using this technique during Delft’s recent project to build a new underground railway, Spruit successfully identified a weak point in a diaphragm wall, which could then be repaired before construction proceeded any further.
The other anomaly detection technique, DTS, relies on an optical fibre sensor to measure temperature variations and can therefore help pinpoint locations where, for instance, clay meets concrete. “DTS shows great potential for a step forward within quality control during diaphragm wall production,” said Spruit, “so will primarily be useful in research settings.”
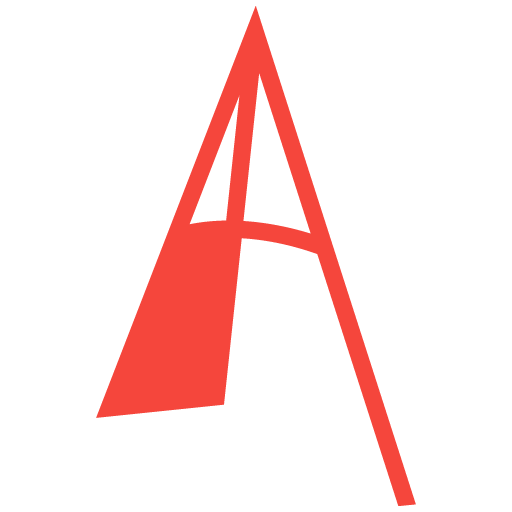
Comments are closed.